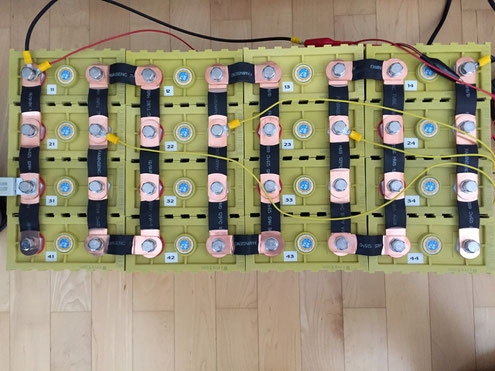
The core of our future energy management solution will be the service battery bank, of course.
After some research I found that the Chinese company Winston was producing batteries well suited for boating purposes.
The battery chemistry of Winston cells has been improved by adding Yttrium to the mix. This results in an increased life time of the cells and also improves resiliency against low temperatures.
While traditional LiFePO4 cells may not be used (charged or discharged) below 0 °C, this is not a problem with the LiFeYPO4 variant. Not something we are currently worried about, but good to know...
Our boat has a 12 V system, and we wanted at least 400 Ah of total battery capacity in the service bank.
For LiFePO4 cells this means four cells in series (resting voltage 3.3 V * 4 = 13.2 V) will do the trick to achieve roughly 12 V system voltage.
After carefully measuring the dimensions of the empty battery box on our boat we tried to find a match with the existing battery package sizes Winston produces.
Unfortunately the 200 Ah (and all larger) batteries were just a tad to high for the box, so we chose the 100 Ah model. 4 cells in parallel (called "4P") will yield 400 Ah @3.3 V, and four of these packs in series ("4P4S") provide the desired system voltage, while comfortably fitting the available space.
There will also be lots of free space left in the box, as the 16 cells are physically much smaller than the old Lead Acid battery bank. The space will be needed for additional electrics such as distribution, fuses and contactors.
The advantage of this 4P4S configuration is that the individual 100 Ah cells are quite small and lightweight (only 3.4 kg per cell), and installing them in a battery cage will be much easier due than heavier and bulkier larger models.
In addition, should one cell go bad later, the whole pack can be rewired to a 3P4S configuration, still yielding 300 Ah (with 3 unused cells as backup, then).
The downside is that a some pack-internal must be done to connect the batteries properly, and physically fixing the batteries in the boat might be a bit more work.
Cell Balancing
Lithium batteries need to be "balanced" in order to work properly. Without going into to much detail this means that it is beneficial for the health of the pack to keep all cells at the same state of charge in order to avoid over- or undercharging individual cells when approaching the top or low end of the pack state of charge. Protecting the cells from such a condition is the job of the Battery Management System, but it is beneficial to bring the pack in a balanced state to avoid premature shut-off of the BMS.
In the top picture you can see the test setup I created at home to balance the cells after I received them via mail order from our dealer LiTrade. Some initial balancing on the individual cells was done by the vendor before delivery, but this will typically not be sufficient after a 4P4S pack has been composed of the cells by the customer.
This is not an article about Lithium battery balancing (there is plenty information on the Internet). But I will summarize some of my steps here.
I decided to perform a top balance, because charging the battery to 100 % State of Charge happens much more often on a sailing boat than discharging the pack completely (in which case a bottom level balance would be more appropriate - such as in electric vehicles).
I arranged the cells in the final configuration, connected them electrically and labelled them so I could reproduce the configuration later. Then I discharged the pack a bit (about 10 Ah) to make room for top balancing.
Once this was done I recharged the pack with a constant 14.4 v (3.6 V * 4) voltage at a charging current of 5 A while keeping a keen eye on the individual cell pack voltages with a digital multimeter.
Whenever I noticed a disbalance (higher voltage of a single cell than the other cells) I manually used a 1 Ohm 25 W resistor directly on the cell terminals to temporarily shunt some charging
current "around" the cell which had reached the ceiling of 3.6 V. I repeated that process with until all cell packs were at an identical voltage of 3.6 V and stopped the charging process. The
whole process took about one hour to complete.
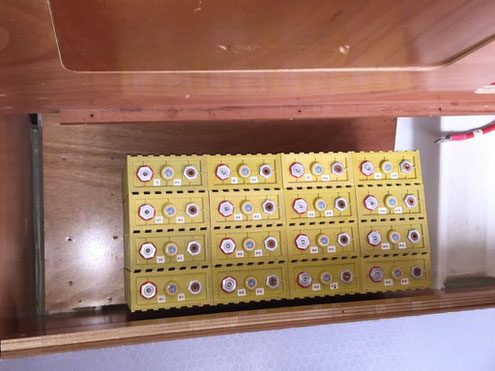
After this was done I discharged the pack to 65 % State of Charge for storage and disassembled the pack, ready to be transported to the boat.
The image shows the designated installation location in the battery compartment. The goal of this dry run was to check available space and arrangement of the battery block.
Write a comment
Cory (Saturday, 24 June 2017 18:40)
Where is the main charge and discharge attached to the pack? It is difficult to determine from the picture posted.
Thanks
Martin Bartosch (Saturday, 24 June 2017 18:48)
Hi Cory,
In this article the pack is wired for top balancing charge with very low current, so you don't see heavy wires in the first image.
Check out https://www.entropypool.de/2015/08/05/designing-a-lifepo4-battery-system-part-4-real-world-implementation/ - you can see the real world wiring there.
Cheers
Martin
Jerome (Saturday, 27 April 2019 21:07)
A much easier way to balance the batteries would be in parallel and use a lifepo4 charger.
Martin Bartosch (Sunday, 28 April 2019 16:30)
As mentioned in the article this is not a post about battery balancing.
The cells had been charged in parallel by the vendor just prior to shipping (that was a service they offer). However, parallel charging does NOT assure that the cells are completely equally balanced. The slight variations of resistance in the paths to the cells in addition to internal cell resistance result in a very similar but not equal state of charge.
For this reason it is useful to assemble the pack in its final configuration and then balance the individual (paralleled) cell packs.
Of course the balancing itself could be done automatically by a LiFePO4 charger with cell sensing, but at the time of the writing I did not have one at home. And I was really eager to see myself how the cells behave when charging.