Choosing a high performance alternator
As previously described, we intended to replace the old alternator with a high performance model which can withstand extended periods of high loads (the LiFePO4 bank will absorb any current you throw at it, overloading most standard alternators quickly) and also produces as much energy as possible to allow us recharging our battery quickly.
After some research and excellent consulting from Richard (RJS Marine) we decided to try the Balmar AT165 alternator (the red component), a very nice design which was supposed to work very efficiently even when running the engine at lower RPMs.
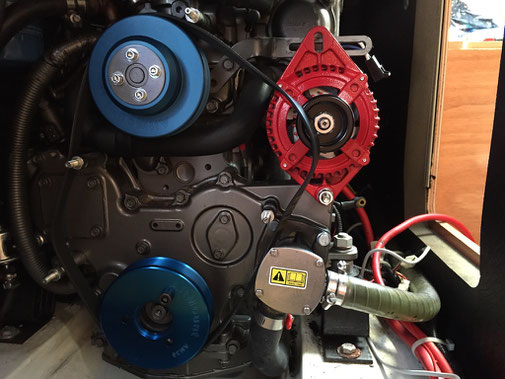
Bad luck with the AT165
Unfortunately it turned out that the terminal layout of the Balmar AT 165 is not optimal for our Yanmar 4JH5E engine. As you can see in this image, the B+ terminal (with a loose cable shoe attached to check the installation) is placed too far inward. The alternator cannot be tilted towards the engine further than this - and this already causes the cable shoe (+) to touch the engine block (-). Definitely not good!
To make matters worse, as you can see this is already almost the extreme outward mounting position as allowed by the tilting arm.
So, no joy with the AT 165, sadly.
Later it turned out that Balmar had addressed this issue by adding a new component to their 2016 product catalog: an idler pulley which was intended to route the belt around the water pump, potentially allowing the alternator to tilt outward to the extreme outward position.
We tried this, but were not convinced by the mechanical compromises we'd have had to accept.
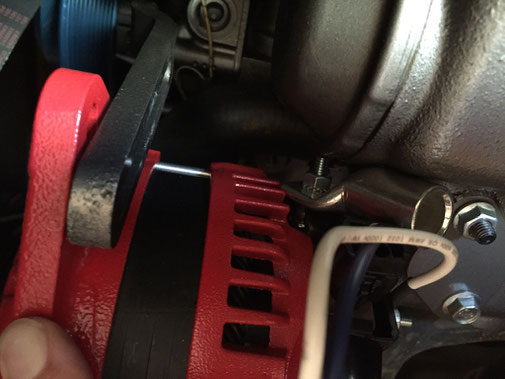
Let's try a Balmar 60 type...
Richard from RJS Marine was very helpful again, he offered to exchange the AT 165 for the older and more conventional Balmar 60 type alternator. Rated at 150 A and less efficient, but with different terminal layout.
So, here we go again, let's mount the Balmar 60 alternator.
As you can see, this time this looks much better. Installation was straightforward and simple, the terminal layout allows cable installation without running the risk of touching the engine block.
Charging the service bank at 114 A. Not quite what we expected, but also not too shabby.
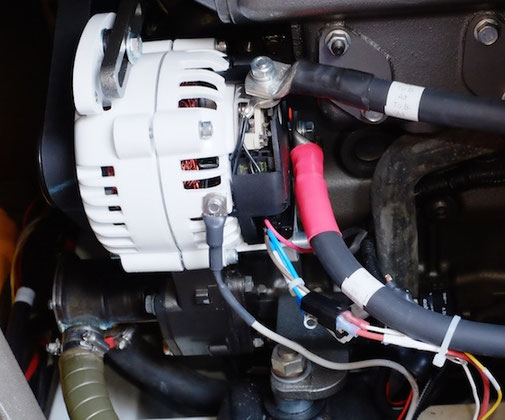
Write a comment
Mark (Monday, 04 July 2016 08:37)
Did you try to rotate the AT165 around its axis, so that the positive terminal would be facing down and outwards?
Martin Bartosch (Monday, 04 July 2016 09:51)
I did not think of this, but I am quite sure it would not have worked.
The foot of the alternator has a M10 bore, but the top is a M8 hole if I am not mistaken (cannot check currently). Hence, reversing is not possible without modifying the alternator.
Otherwise it would have worked, I think, the terminal layout should fit if were reversed.
Dia Claro (Monday, 06 February 2017 15:11)
I am in fact glad to read this webpage posts which contains plenty of valuable facts, thanks for providing such data.
GURDOGAR SARIGUL (Wednesday, 09 March 2022 23:24)
Sorry guys, but this could have been easily solved by removing and little bending of the upper arm attached to the body of the engine. Turning upside down would not really solve this problem, bcs two holes are same distance to the center of the motor when you turn upside down nothing will be different.
Martin Bartosch (Thursday, 10 March 2022 11:07)
I doubt that this would work. First of all I would refrain from permanently modifying parts of the engine. This would also mean that the alignment of the pulleys would be totally off. You'd have to extend the pulleys of the water pump and of the engine main shaft forward and carefully align with the alternator pulley. Due to increased leverage effect this would also increase the lateral force on the drive shaft (due to the belt tension), adding wear on the bearings.
Also, this would mean that the engine cover would have to be permanently removed.
All in all not an option I would consider.